What is activity-based budgeting?
Activity-based budgeting (ABB) is a top-down financial budgeting method focusing on resources allocated to individual budgeting activities instead of departments or products.
With an activity-based budgeting approach, you break down each business activity into tasks and assign costs for each task. This helps you determine the funding needed to support each task performed.
Examples of business activities include:
- Purchasing materials and supplies for production, such as raw materials, components, and parts.
- Manufacturing processes for producing goods or services, like quality control checks and assembly workflows.
- Marketing activities like advertising campaigns, sales promotion efforts, and hiring.
- Research and development efforts such as product testing.
Breaking these processes down and identifying cost drivers allows for greater control over financial decisions and better visibility into how funds are used.
Activity-based budgeting can also help organizations identify cost drivers and redundant processes to streamline business operations and maximize resource efficiency.
What’s a cost driver?
A cost driver is a factor that influences the cost of doing business, from production and manufacturing to marketing and hiring. Examples of cost drivers include:
- The number of units produced in a period
- The number of direct labor hours involved in a project
- The machine hours used in a week
- The square footage of factory space occupied
- The cost of hiring an employee or contractor in the current market
The more of each cost driver you use for producing an item or a service, the higher the total associated costs with that item.
Breaking down these costs is the first step in reducing the cost of producing goods or providing services.
Resource allocation based on activities
Resource allocation based on activities, a core principle of Activity-Based Budgeting (ABB), ensures that financial resources are aligned with operational demands within an organization.
Unlike traditional methods, ABB prioritizes resource allocation according to specific activities' requirements, optimizing resource utilization and directing investments towards activities that contribute most to organizational goals.
This approach enhances transparency and accountability in budgeting, facilitating informed decisions and driving efficiency in financial planning and analysis processes.
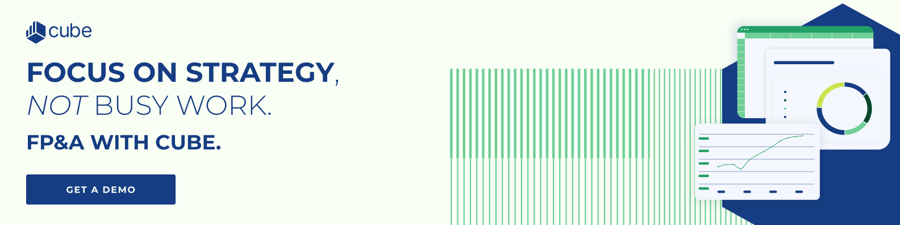
Why do companies use activity-based budgets?
Controlling costs is imperative to preserving revenue, so companies always look for creative ways to avoid overspending. This is why activity-based budgeting is such an effective budgeting approach.
Understand expenses incurred: Traditional methods of budgeting rely on the previous year’s data to establish the basis for changes. To perform activity-based budgeting, finance analyzes every cost from the ground up. Activity-based analysis occurs without consideration of the previous year's budgeting activities to justify every cost on its merit.
Improve business efficiency: Inefficiency creates a stealthy burden on cash. Using budget analysis to reduce inefficiencies in your process is an excellent way to ensure your business only spends money where it needs to.
Activity-based budgeting is an in-depth approach to planning future spending. It scrutinizes every expenditure at every step of the process to identify places to trim the fat and improve your business processes.
Companies use activity-based budgeting to get a deep understanding of and control costs. By breaking down costs into separate activities, companies can allocate resources more effectively, improve financial performance, and identify redundant or unnecessary activities.
Activity-based budgeting also helps ensure that the most important activities allocate the right budget. It can help uncover opportunities for cost savings It helps managers to track actual spending versus budgeted amounts and compare spending across different departments or locations.
You might consider using activity-based budgeting if:
- Your organization is in cost-cutting mode
- There are visibility challenges in your spending
- You’re restructuring the entire organization
- Traditional method of budgeting hasn't been working well for you
What are the benefits of activity-based budgeting?
Companies turn to activity-based budgeting when they need a better handle on spending. This type of budgeting exercise helps young companies manage their costs from the start and established companies bring expenses under control when needed.
Full spend visibility: Activity-based budgeting creates a granular view of every process that crates cost or revenue for the company. This level of detail takes time, but the effort pays considerable dividends in cost savings.
Budgetary control: Making decisions for the budget based on cost drivers enables better control over your spending. It allows companies to understand exactly what drives spend (and budget inflation) for better cash performance.
Competitive advantage: Reducing costs and optimizing processes allows you to produce goods more efficiently and retain more profit. Activity-based budgeting shows you where to improve and what’s essential to your process.
What are the challenges of activity-based budgeting?
The biggest challenge of activity-based budgeting is when you have many new activities or variables—like new business locations—that you can't account for or that skew your numbers.
Time-consuming: The granular detail of an activity-based budget process requires significant research and analysis and can become time consuming. This budgeting system takes more time and labor investment than other planning methods.
Expensive: The level of research required to complete an activity-based budget means that many stakeholders will invest time in preparing data. This has associated costs not experienced with traditional budgeting. However, the cost benefits of this exercise may well justify the investment.
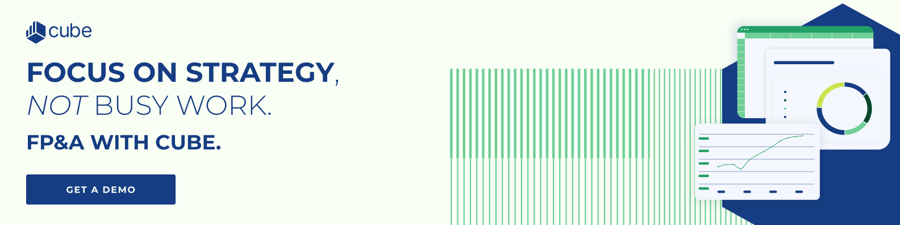
How do you create an activity-based budget [with example]?
An activity-based budget breaks down each element of an organization’s spending into its component activities.
This includes:
- Analyzing direct expenses, such as materials purchasing and machine hours
- Calculating overhead costs and indirect spend associated with each activity.
By breaking down spending in this granular manner, organizations more accurately determine their total budgets for each activity and adjust accordingly.
To build an activity-based budget, use these steps.
1. Identify expense and revenue activities
Break down each process into its steps. For each step in the process, identify the expense it generates.
For example, manufacturing a product isn’t just “buy materials, make products.” The process is more complicated.
- Create an RFP to source materials.
- Purchase the raw materials and supplies needed for the product.
- Create components from materials and parts.
- Use those components to build the product.
- Test the product to ensure it meets quality standards.
- Package the product in appropriate sleeving and materials.
- Ship out the finished product.
- Track and record sales on delivered products.
If a company estimates it needs to build 50,000 units of a product (based on its previous year of sales), it must complete each of the above steps for every item. Each repetition of the above steps has an associated cost.
2. Estimate the cost drivers necessary for activities
An activity-based analysis looks at each step in this example to identify every cost driver associated with production, including materials, equipment, labor hours, and utilities.
In our manufacturing example, the product requires:
- Several machinists at market wage rates to keep up with expected production.
- A dedicated production line with a specialty machine.
- Specialized packaging for shipment.
All these factors affect the price of production for each unit you produce.
So, we break down the product example above into its costs:
- Machining operation: 500 machine hours at $5/hour = $2,500
- Labor costs: 500 hours at $15/hour = $7,500
- Materials costs: $2 per unit = $100,000
- Shipping costs: $.5 per unit = $25,000
From here, you can calculate the total and per-unit cost of producing your item.
3. Calculate the total cost
Once you have the figures for every piece of activity, you can calculate the total cost and per-unit cost of production:
Total cost: $135,000 for 50,000 units
Per-unit total: $2.70 per unit cost
4. Identify improvements and unnecessary costs
With the above information, the organization can evaluate activity performance to become deeply familiar with its granular costs and use the information to cut individual cost drivers, such as:
- Sourcing less-expensive materials for production
- Improving shipping expenses through volume negotiation
- Optimizing machine outputs to produce items faster
This step-by-step analysis is intensive but effective to drive costs down and under control. This process helps organizations reduce costs for any business activity: Manufacturing, sales, marketing, recruiting, etc.
Best practices for successful activity-based budgeting
In this section, we'll explore key strategies for achieving success with ABB, from engaging stakeholders to leveraging technology and fostering a culture of collaboration.
Piloting: Start with pilot projects or smaller-scale implementations to test the effectiveness of ABB before scaling up.
Monitoring: Continuously monitor and evaluate ABB processes to identify areas for improvement and make necessary adjustments.
Training: Invest in training and skill development for employees involved in ABB implementation to ensure they have the necessary expertise.
Culture: Foster a culture of collaboration and communication to facilitate the successful implementation and ongoing management of ABB.
Technology: Utilize technology and software solutions to streamline ABB processes and improve data accuracy and analysis capabilities.
Review: Regularly review and update ABB methodologies and assumptions to ensure they remain aligned with organizational goals and objectives.
Using Cube for activity-based budgeting
As you can see, activity-based budgeting can be a powerful strategy.
What about you? Are you going to try activity-based budgeting at your company this year?
If you're wondering about the logistics, like getting all your actuals together, then you should consider Cube.
Cube connects to your source systems (like your ERP) and matches, validates, and de-dupes you data so you fetch it into your Excel spreadsheet in a single click and start budgeting.
Interested in hearing more? Request a free demo below:
